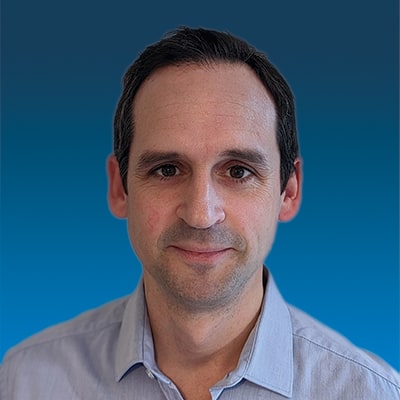
In this series of short technical articles, we look at various topics that illustrate the complexity of renewables as a concept within the ongoing energy transition. Here, PSC’s Adam Maloyd looks at the implications of using fault ride through to mitigate the adverse effects of faults in the modern grid.
Fault ride through
An electricity network is a dynamic system, made more so with the increase of renewable resources like wind and PV using inverter-based resources (IBRs) that further complicate the dynamic response of the power system due to the decrease in synchronous inertia and faster but less predictable response of IBRs.
Beyond electricity generation, an extensive array of diverse technologies and many parts of the physical infrastructure enable electricity to be transmitted and distributed to the consumer. In this vast and complex system, inevitably, faults will occasionally occur. Therefore, an electricity network must be resilient and designed to survive faults and significant changes in the balance between supply and demand.
One method to mitigate the negative effect of faults on a network is fault ride through (FRT).
FRT in the modern grid
FRT is the capability of generators to withstand and recover from short-term disturbances, such as voltage sags caused by network faults; hence FRT is also often known as low voltage ride through (LVRT).
FRT is an important feature for ensuring the stability and reliability of electrical networks, especially those with a high penetration of renewable energy sources, which can negatively impact the stability of frequency and voltage in the grid.
Previously during faults, smaller renewable generators would disconnect from the grid to avoid islanding part of the network; however, with the increasing size and penetration of renewables, if a large number of renewable generators suddenly disconnect during a fault, the situation on the network could become more severe. Therefore, generators must remain connected, support active and reactive power injection during disturbances, and support the system to maintain overall stability through FRT.
Grid codes
The FRT requirements for a generator are specified in the “Grid Codes,” which outline the connection requirements to ensure the power supply’s security, reliability and quality.
A grid code outlines the minimum technical requirements for generators and HVDC connectors to connect to the grid, including fault behavior requirements, i.e., FRT. Therefore, it is important to know the connection requirements in advance and to complete studies to demonstrate that all grid code requirements are met. It should also be noted that grid codes are not static, they are reviewed and updated as the power system requirements evolve and network characteristics.
Depending on the type of fault and generator, the grid code defines a voltage, which the generator must maintain to avoid a total voltage collapse. An example of this requirement is shown in the figure to the right.
Additionally, the generator may be required to inject reactive power into the network during a fault to support voltage recovery. So studies must also be completed to demonstrate that during a fault, the reactive current output of the generator increases and does not drop. Generally, generators are required to prioritize active power support with any remaining capability as reactive support; however, primarily providing reactive current may be more beneficial to the network and is worth assessing.
Synchronous generators
Synchronous generators (i.e., where the waveform is synchronized with the rotation of the generator as in traditional generation) have inertia to strengthen the grid and also have a “natural” response by adjusting the machine’s rotor angle and injecting a large amount of current into the grid during voltage sag. This is from the rotor angle changing and the machine seeking to redress this imbalance.
It is important that synchronous generators have a good dynamic response so they can quickly and accurately respond to changes in the grid frequency and voltage during and after a fault. This is typically achieved through high-quality excitation systems and power electronics. There are several ways in which synchronous generators can be designed to improve their fault ride through capabilities, including the use of stator and rotor windings with low resistance and high fault current carrying capability, the inclusion of protective devices such as circuit breakers and fuses, and the use of power electronics, such as thyristors, to control the flow of current to the generator.
Wind turbines FRT
With the dramatic increase in global wind generation, turbines must meet specific criteria to avoid damage or mal-operation during low-voltage events, including grid code FRT requirements.
Wind turbines include power electronics for enhanced control. These are either fully converter-connected or doubly-fed induction generators (DFIGs), with partial power back-to-back converters where a portion of the power generated by the rotor is sent to a power converter, which controls the speed of the rotor and the amount of power sent to the grid.
Although a wind turbine has inertia due to the kinetic energy in the rotating blades, this inertia is “lost” as the power electronics essentially decouple the generator from the network.
IBR FRT
The growth of IBRs has increased the complexity of converter controls, . Unlike synchronous generators, IBRs will not automatically supply an instantaneous injection of fault current upon fault inception; there may be a delay (~10-20ms) before the IBR fault current (~1.2 x rated current) is output. Therefore, the control system must be designed so that the device responds in a way to meet the grid code requirements.
For IBRs, the power output can be configured depending on the design of the converter’s control system. Generally, the primary purpose is to protect the switching devices (Insulated-gate bipolar transistors, or IGBTs) from excessive currents during faulty conditions. One way to address this issue (other than overrating the IGBTs) is to improve or replace the controllers for converters, which are an important component in connecting renewable resources to the grid.
The important thing to note when building the model is that for the simulation to be carried out, it is essential to have a model of the inverter (or generator, governor and AVR) that can be implemented within whichever modeling package being used. Without this data from the manufacturer, modelling assumptions may be made, though these may not provide accurate results.
The control strategy of the IBR should also be incorporated into the dynamic model, as this greatly affects its dynamic performance, unlike synchronous generators, whose transient behavior is greatly affected by the physical properties of the machine.
FRT studies shown above are root mean square (RMS) simulations, which provide good results for electromechanical phenomena. As networks become more highly IBR based, as previously mentioned, RMS simulations may not be enough and electromagnetic transient (EMT) studies using software such as PSCAD, may be required to fully model the control behaviors of the IBR and interactions between devices.
Summary
FRT is a critical aspect of power system design and operation, and various technologies and techniques are used to ensure that power systems can withstand and recover from fault events.
If you’re looking for help with your power system studies, here’s more information about our capabilities. Please contact us to get started!
Series links
The complexity of renewables, Part 1 – PSC Consulting
The complexity of renewables, Part 2 – PSC Consulting
The complexity of renewables, Part 3 – PSC Consulting
The complexity of renewables, Part 4 – PSC Consulting
The complexity of renewables, Part 5 – PSC Consulting
The complexity of renewables, Part 6 – PSC Consulting
The complexity of renewables, Part 7 – PSC Consulting
The complexity of renewables, Part 8 – PSC Consulting
The complexity of renewables, Part 9 – PSC Consulting