More than 800 participants and 60 exhibitors worldwide gathered at Centre de Congrès de Lyon on 19 – 21 June for the Jicable conference, including a delegation from PSC UK, including Rose Urban, Hugo Hui and Joe Oliver. The conference is a major international event focused on insulated power cables and associated products. Other than allowing numerous cable engineers to share their latest research and experience, Jicable is a forum for discussion on how cables play an important role in power grids now and in the future. Here are our main takeaways from the conference.
Global energy demands drive cable growth
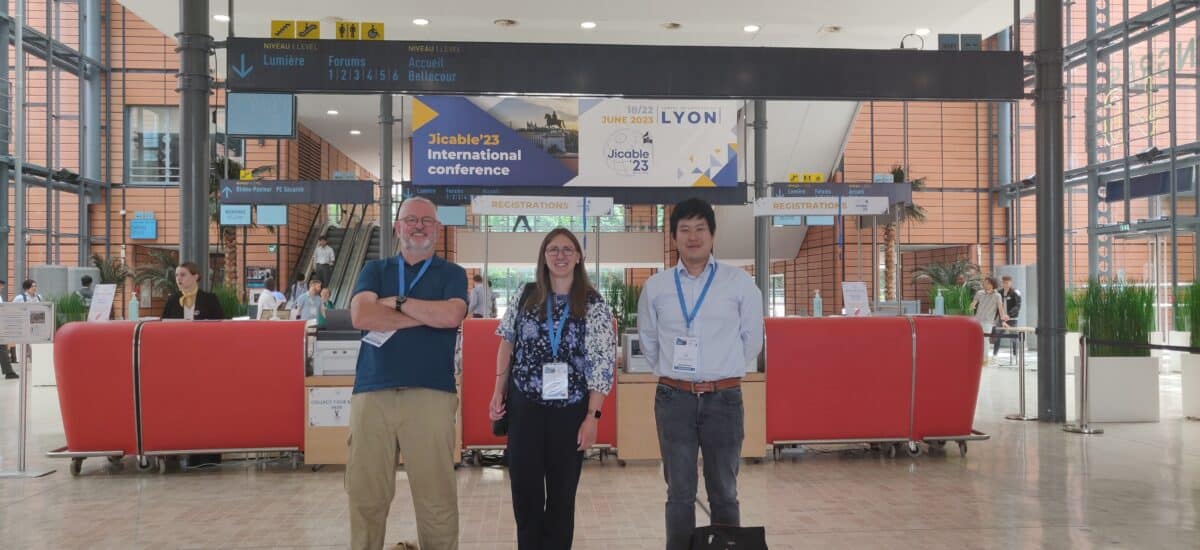
(L-R): PSC UK’s Joe Oliver, Rose Urban, Hugo Hui at Jicable ’23 in Lyon, France.
The demand for cables is higher than ever. To meet the increasing global energy demand and energy efficiency targets, numerous high-profile renewable energy and interconnector projects are being developed, such as the North Sea Wind Power Hub and Xlinks Interconnector. These projects require very long and large cables to transmit power efficiently to large cities from remote energy sources. It is forecasted by ENTSO-E that 46,000 km of cables are needed in Europe alone in the coming decade in order to meet the demand.
Environmental impact: lead-sheathed cables
One of the major immediate challenges for submarine cables may come from restrictions on the use of lead. Lead is known for toxicity that harms the human body and the damage it can cause to the ecosystem if released into the environment. Although there has been evidence that cables do not release lead to the environment, an ongoing authorization process by the European Chemical Agency (ECHA) could restrict or even forbid the use of lead entirely.
As submarine cables are installed at great depths in the ocean, the mechanical and chemical properties of lead enable the cables to be protected against harsh external factors such as high water pressure and corrosive seawater. In addition, the flexibility of lead makes it useful for cable installations. The worst outcome of the authorization process is that no manufacturing and installation of power cables with a lead sheath – including repairs – would be allowed from 2028. Currently, no alternative material is available that can replace or surpass the performance of lead, leading to the risk of major undersea projects being halted at a time when they’re needed most.
Carbon emissions from copper and cable manufacture
The use of copper in cables also has an environmental impact. Copper is a highly conductive metal that is commonly used for manufacturing cable conductors. Aluminum can also be used. However, the mining and refining processes of copper use a great deal of energy. Copper accounts for approximately 80% of carbon emissions related to the cable manufacturing process [Source: Jicable 23 C10-6 Presentation: Innovative Trends and Solutions for EHV XLPE Insulated Cable Systems].
For AC cables, designs such as Milliken cables (or segmented cables) improve the conductivity of cables and reduce the amount of conductor needed. Lowering the DC conductor resistance doesn’t necessarily mean that the AC conductor resistance will always be improved.
The environmental impact of transporting cables from factories to the installation site is commonly neglected [Source: Jicable 23 C10-6 Presentation: Innovative Trends and Solutions for EHV XLPE Insulated Cable Systems]. The amount of carbon emission related to transport varies according to the distances that cables need to be transported. Comparing long-distance delivery to local delivery, for example, the amount of transport-based carbon emissions by transport can vary by 500%.
To reduce the overall environmental impact of cable deliveries, it could be useful for end users to factor in the combined carbon emissions from the extraction of raw materials through manufacturing to transport and final delivery when assessing a tender for supply.
Cable testing
For long HVDC cables, the power required for AC voltage testing is very significant, being proportional to the length of the cable cubed. Germany’s DIN IEC 62895, for example, requires AC voltage tests, which results in the screen current being significant and for an HVDC cable, the screen may not even have been designed for this level of current. Cable systems designers need to be sure when designing a cable system, that it can be tested.
In case of failure during testing, safety is also an issue to be considered. With AC turntable testing, there are magnetic effects due to the coiled nature of the cable that need to be considered as well as thermal issues due to heat generation in the screen.
Improving manufacturing line speeds
Improving the line speed during insulation extrusion was another topic of conversation during the conference. Potentially higher line speeds of up to 25% – along with an improvement in ovality – could be achieved by replacing the original heating tube with two high-temperature segments and applying a high-temperature impulse during the curing process. This translates into material savings and was reported to have been verified on hundreds of kilometers of HV cable.
Other considerations
The increase in global demand for cables, changes in materials for use in cables due to environmental concerns, increases in voltage and conductor design to enable higher power transfer and optimizations in production processes all put an increased requirement on there being suitable tests to qualify the cable system and ensure it’s quality over the lifetime. CIGRE Technical Brochure 852 has recently been published which includes a table identifying tests required for qualification of changes or modifications in a qualified cable system.
PSC has the expertise to advise on the environmental impact of cables, the optimization of cable systems at the design stage, and the impact of existing qualification tests covering the system. Contact us for more information.